By optimizing the installation process, we reduce downtime and ensure that projects are completed on schedule.
The rapid expansion of offshore wind energy is driving demand for specialized installation vessels capable of handling the increasing size and weight of wind turbine foundations. As turbines grow in capacity, installation vessels face greater challenges, especially with the expanding range of offshore locations requiring operability in deeper waters and challenging environments. 5,000-ton monopiles measuring 15 meters in diameter and over 120 meters in length are being projected as future foundation sizes and weights, necessitating advanced capabilities. GustoMSC, a leader in the field, has developed sophisticated analysis frameworks for both jack-up and vessel-based monopile installations, ensuring safe and efficient deployment. Our expertise allows customers to rely on us for comprehensive engineering consultancy in offshore monopile installation using either a jack-up or a vessel.
GustoMSC is a well-known industry leader in the design of vessels used in the transport and installation of wind turbines and foundations. GustoMSC has recently been developing the capability to perform operability analyses of installing large monopiles from both jack-ups and vessels. This two-body analysis capability allows owners and operators to specify the requirements for the installation equipment including static or motion compensated grippers and confidently deploy their jack-ups and vessels to install monopiles safely and efficiently. GustoMSC recognizes that monopile installation from floating vessels present unique installation challenges and is keen to work with its customers to resolve these challenges. This article focuses on GustoMSC’ s newly gained capability in simulating vessel-based monopile installation.
Back to Overview
October 2024
Reading time: 2,5 min
Safe and Efficient Installation of Next Generation Monopiles
InSide
A storytelling platform about our offshore challenges
Vessel-based monopile installation
GustoMSC
Karel Doormanweg 35
3115 JD Schiedam
The Netherlands
The Pioneers of Offshore Engineering
GustoMSC is recognized for providing advanced design & engineering consultancy for mobile offshore units and reliable equipment.
We enable and support safe and efficient operations at sea, contributing to a sustainable future.
Please subscribe to the newsletter so we can keep you up to date with our latest stories and extra news updates.
Subscribe
Share article
Back to Overview
Enhanced Operational Efficiency
Our analysis framework offers several key advantages:
1 | 3
2 | 3
Accurate risk assessments and real-time monitoring allow us to mitigate potential hazards, ensuring the safety of both the crew and the environment.
Increased Safety
3 | 3
Better understanding and management of environmental constraints lead to significant cost savings throughout the project life cycle.
Optimized Costs
Contact us for a presentation
Mode 3
Mode 4
Mode 8
Mode 9
Mode 5
Mode 6
Mode 7
1 | 3
2 | 3
Phase 2
Phase 3
Ball joint
We believe that these detailed time domain simulations have revealed insights into the installation operation which will help customers to increase the operability and safety of their installation. We look forward to working with customers as they plan and execute their monopile installation projects.
Sketch of the restoring forces of the operation.
Note the crucial role of the motion-compensated gripper in ensuring monopile verticality.
Selected modes from a modal analysis performed on the multi-body vessel-monopile-gripper system. NB: gripper not visible in these images.
Share article
GustoMSC
Karel Doormanweg 35
3115 JD Schiedam
The Netherlands
nov.com/gustomsc
info.gustomsc@nov.com
+31 (0)10 2883 000
The Pioneers of Offshore Engineering
GustoMSC is recognized for providing advanced design & engineering consultancy for mobile offshore units and reliable equipment.
We enable and support safe and efficient operations at sea, contributing to a sustainable future.
Please subscribe to the newsletter so we can keep you up to date with our latest stories and extra news updates.
Subscribe
The vessel-based analysis framework is a time-domain simulation model featuring a vessel on DP, a monopile, and a motion-compensated gripper. The most important feature of the coupled time-domain simulation model is the appropriate description of the complex interaction between vessel and monopile hydrodynamics, DP controller, and gripper controller. The time domain model features two controllers running in parallel. The DP controller ensures acceptable vessel motions whilst the gripper controller aims to keep the monopile at its target position, thereby ensuring its verticality. The gripper controller achieves this by compensating for vessel motions and counteracting monopile loads. By modelling both controllers, it is possible to simulate motions and loads on the vessel, monopile, and gripper. The results of such simulations can be used to verify the design of the DP system and the motion compensated gripper such as dimensioning the required available stroke or the maximum delivered force. Efforts have been made to verify components of this numerical model to ensure that the dynamics of this multi-body system are properly modelled. The vessel, monopile, and gripper have been exposed to current, wind, and wave excitation and their resulting motion response has been computed in time domain. The gripper controller strategy that emerges from these simulations suggests that different phases of the operation requires different strategies and that careful tuning is required to optimize the overall operability.
GustoMSC is a well-known industry leader in the design of vessels used in the transport and installation of wind turbines and foundations. GustoMSC has recently been developing the capability to perform operability analyses of installing large monopiles from both jack-ups and vessels. This two-body analysis capability allows owners and operators to specify the requirements for the installation equipment including static or motion compensated grippers and confidently deploy their jack-ups and vessels to install monopiles safely and efficiently. GustoMSC recognizes that monopile installation from floating vessels present unique installation challenges and is keen to work with its customers to resolve these challenges. This article focuses on GustoMSC’ s newly gained capability in simulating vessel-based monopile installation.
The rapid expansion of offshore wind energy is driving demand for specialized installation vessels capable of handling the increasing size and weight of wind turbine foundations. As turbines grow in capacity, installation vessels face greater challenges, especially with the expanding range of offshore locations requiring operability in deeper waters and challenging environments. 5,000-ton monopiles measuring 15 meters in diameter and over 120 meters in length are being projected as future foundation sizes and weights, necessitating advanced capabilities. GustoMSC, a leader in the field, has developed sophisticated analysis frameworks for both jack-up and vessel-based monopile installations, ensuring safe and efficient deployment. Our expertise allows customers to rely on us for comprehensive engineering consultancy in offshore monopile installation using either a jack-up or a vessel.
October 2024
Reading time: 2,5 min
Safe and Efficient Installation
of Next Generation Monopiles
InSide
A storytelling platform about our offshore challenges
Vessel-based Monopile Installation Tool
1 | 3
2 | 3
3 | 3
The vessel-based analysis framework is a time-domain simulation model featuring a vessel on DP, a monopile, and a motion-compensated gripper. The most important feature of the coupled time-domain simulation model is the appropriate description of the complex interaction between vessel and monopile hydrodynamics, DP controller, and gripper controller. The time domain model features two controllers running in parallel. The DP controller ensures acceptable vessel motions whilst the gripper controller aims to keep the monopile at its target position, thereby ensuring its verticality. The gripper controller achieves this by compensating for vessel motions and counteracting monopile loads. By modelling both controllers, it is possible to simulate motions and loads on the vessel, monopile, and gripper. The results of such simulations can be used to verify the design of the DP system and the motion compensated gripper such as dimensioning the required available stroke or the maximum delivered force. Efforts have been made to verify components of this numerical model to ensure that the dynamics of this multi-body system are properly modelled. The vessel, monopile, and gripper have been exposed to current, wind, and wave excitation and their resulting motion response has been computed in time domain. The gripper controller strategy that emerges from these simulations suggests that different phases of the operation requires different strategies and that careful tuning is required to optimize the overall operability.
Anand Ashok
Senior Engineer at GustoMSC
For more information about our vessel-based monopile installation analysis framework, feel free to contact Anand or Estela:
Related publication
Inside Out: Integrated Design Process
Fulfilling the industry’s ambitions together. There is a constant demand to stretch the boundaries in the offshore wind-turbine installation market...
Read more
Estela Sanz Horcajo
Engineer at GustoMSC
Monopile mass vs offshore construction start year
Total wind demand international
Share of demand met by vessel supply
Source: 4COffshore
Source: Clarksons
Source: Spinergie
The analysis framework for vessel-based monopile installation
3 | 3
Gripper setting
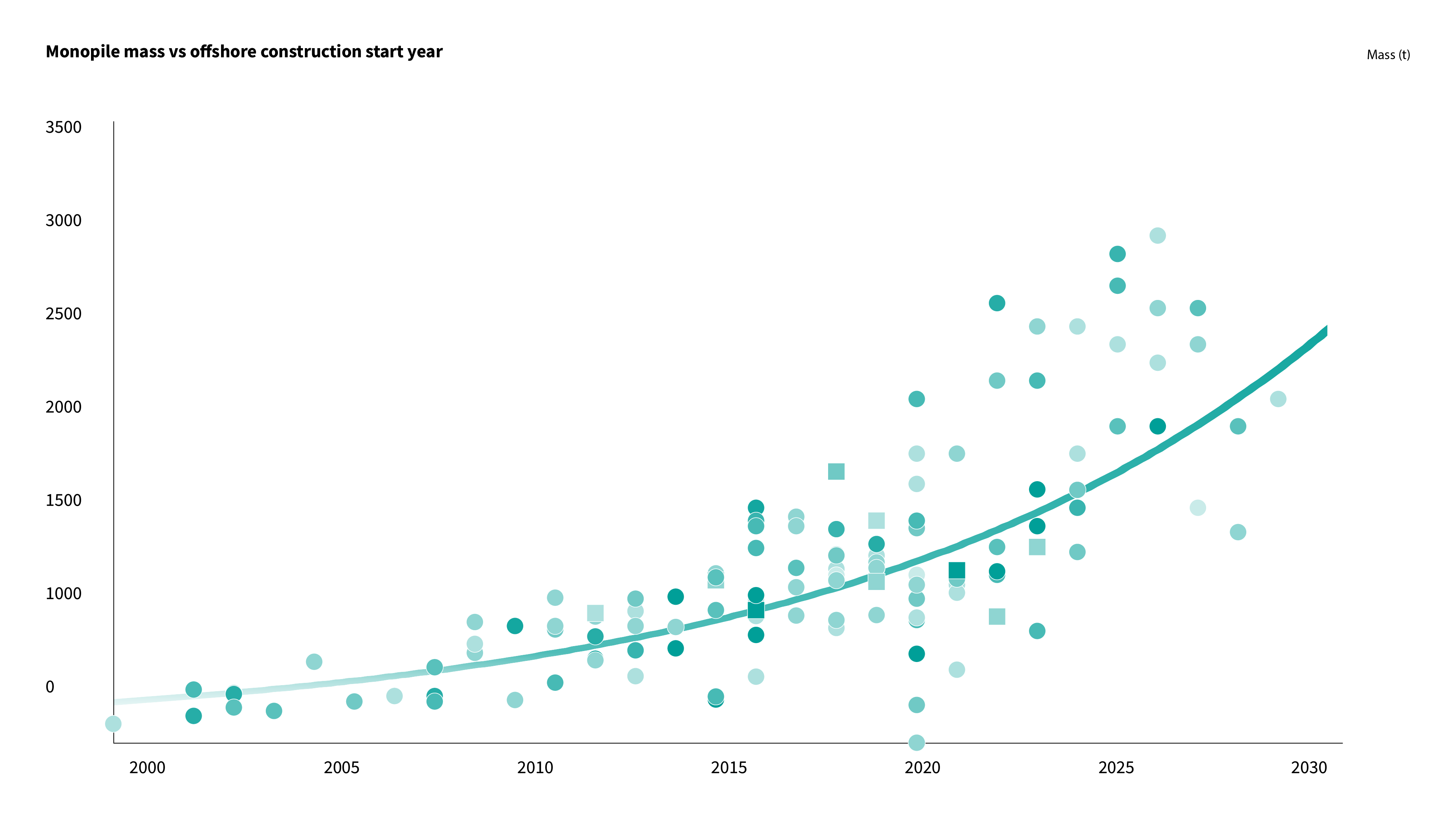